Адсорбционные насосы GHS Pumps
Адсорбционные насосы собственного производства, разработанные совместно с немецкой компанией GHS Pumps — стандартные адсорбционные насосы и специальное изготовление насосов для самых разных приложений.
Адсорбционные тепловые насосы и чиллеры – последние разработки в области материалов и компонентов.
Введение: разработка тепловых насосов и чиллеров, в которых используется адсорбция хладагента на адсорбенте, оказалась привлекательной возможностью использования тепла, доступного при более высокой температуре (HT, например, отходящее тепло или солнечное тепло), либо для производства холода, либо для производства холода. для преобразования тепла от низкотемпературного (LT) источника тепла в среднетемпературный уровень для отопления. Аспекты, которые необходимо принять во внимание, следующие: Выбор рабочей пары (адсорбционный материал и хладагент) в соответствии с их адсорбционным равновесием с учетом требований применения (температура источников/поглотителей тепла, доступность, стабильность). Проектирование адсорбционного теплообменника путем балансировки различных сопротивлений тепло- и массообмена. Проектирование испарителя/конденсатора вместе с концепцией модуля. Критериями оптимизации производительности являются удельная мощность на объем или массу в зависимости от того, является ли пространство или вес ограничивающим фактором в рассматриваемом применении, а также коэффициент производительности (COP), который является мерой эффективности адсорбционного модуля. Поскольку при работе адсорбционных тепловых насосов и чиллеров эти два свойства ведут себя противоречиво, существует множество способов найти усовершенствованные решения.
Обзор некоторых последних разработок в области адсорбционных модулей и их компонентов для адсорбционных тепловых насосов и чиллеров и материалы для тепловых насосов и чиллеров.
В течение последних лет для адсорбционного преобразования тепла в приложениях, близких к рыночным, использовались в основном три класса адсорбирующих материалов: различные силикагели, цеолиты/зеотипические материалы (например, SAPO-34) и активированные углероды. В качестве рабочих тел использовались преимущественно вода, метанол и аммиак. В последние годы для этих целей были специально разработаны материалы металлоорганического каркаса (MOF), некоторые из которых теперь также доступны в коммерческих масштабах. Другим классом материалов, получившим внимание, являются гидраты солей или аммиаты солей и композиционные материалы, включающие эти соли. Показано, что S-образная изотерма удобна для применений теплового преобразования. Другими основными параметрами, которые необходимо проверить для соответствия материала конкретному применению, являются: поглощение рабочей жидкости при граничных температурах цикла, стабильность, доступность, стоимость, форма соединения с теплообменником (гранулы, склеивание, покрытие, прямой синтез). Особое внимание уделено формованию адсорбентов и контактированию их с теплообменником с целью получения адсорбционного теплообменника. Гранулы адсорбента можно приклеить к теплообменнику или пропустить этап грануляции и нанести порошок адсорбента непосредственно на теплообменник. Нанесение адсорбента на теплообменник позволяет увеличить площадь теплового контакта между адсорбентом и поверхностью нагрева, сохраняя при этом хорошую доступность из газовой фазы. Ключевым компонентом здесь является связующее, выполняющее роль клея между частицами адсорбента и поверхностью нагрева. металлическая поверхность теплообменника. Предложено использовать силиконовые связующие для повышения термостабильности и сравнены различные типы силиконовых связующих и исследовано влияние толщины покрытия на характеристики адсорбера. Прямая кристаллизация адсорбционного материала на поверхности теплообменника показана для различных подложек и адсорбентов. С помощью этого метода синтез адсорбента и покрытия теплообменника можно выполнить всего за один этап, но изменения в сочетании материалов реализовать гораздо сложнее. Полученные покрытия имеют ограниченную толщину (4–230 мкм ), но имеют более высокую плотность, чем покрытия на основе связующего. В следующем разделе будут представлены последние разработки в области адсорбционных теплообменников как со связующим, так и с прямым покрытием.
Концепции теплообменников.
в адсорбционных тепловых насосах и чиллерах используются теплообменники для различных целей: испарение/конденсация и адсорбция/десорбция рабочей жидкости соответственно. Эти процессы фазового перехода требуют различных характеристик теплообменников. Поэтому обзор концепций теплообменников будет дан отдельно для испарителя/конденсатора и сорбционного теплообменника.
При разработке адсорбционных теплообменников (AdHEX) необходимо учитывать множество требований для достижения цели высокой удельной мощности и КПД в циклической работе между высокой и средней температурой уровень. Стандартные трубчато-ребристые теплообменники используются в коммерческих продуктах, в которых используется конфигурация со свободным слоем, иметь гранулы, наклеенные на поверхность ребер, или ребра с покрытием для объединения адсорбционного материала с теплообобменником.
«Идеальный» теплообменник, используемый в качестве адсорбера, должен иметь бесконечную площадь поверхности контакта с адсорбент, отсутствие сопротивления теплопередаче внутри самого теплообменника и вместе с теплоносителем с нулевой тепловой массой и механической прочностью, позволяющей выдерживать давление, возникающее в системе, а также
Недавно несколько теплообменников жидкость-воздух (пластинчато-ребристый теплообменник, см. рисунок 1) были покрыты покрытиями на основе связующего вещества различной толщины и исследованы на предмет их динамических свойств.
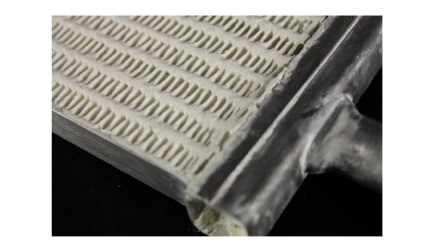
Рис. 1. Пластинчато-ребристый теплообменник с покрытием на основе связующего.
В результате измерений производительности была обнаружена аналогичная плотность мощности, как это также известно из других исследований, как для адсорбционных теплообменников со связующим покрытием [20], [22], так и для конфигураций с мелкими рыхлыми зернами [9], [23]. Толщину адсорбентного покрытия можно увеличивать практически до полного заполнения теплообменника без существенного снижения объемной удельной мощности. Лишь когда доступность поверхности покрытия для пара становится ограничивающим фактором (засорение путей распространения пара), удельная мощность начинает падать.
Волоконный теплообменник с прямым адсорбентным покрытием
Метод прямого нанесения SAPO-34 на алюминий методом частичного преобразования носителя (PST) 1 приводит к получению очень компактных слоев адсорбента с плотностью 1500 кг/м³ и толщиной слоя около 20 – 100 мкм [24]. Таким образом, основным требованием к теплообменнику с таким покрытием является высокая площадь поверхности для получения достаточно высокой массы адсорбента внутри адсорбционного теплообменника. Перспективной подложкой для этого метода покрытия оказались спеченные структуры из алюминиевого волокна [25] с площадью поверхности 6000–9000 м²/м³. С пористостью 70 – 80 % и теплопроводностью 8 – 10 Вт/мК.
Перед проектированием адсорбционного теплообменника были исследованы адсорбционные свойства различных вариантов структуры волокон (пористость и толщина структуры спеченного волокна), а также толщина покрытия [26]. Геометрия плоскотрубного теплообменника в сочетании с этим волокнистым материалом образует компактный адсорбционный теплообменник. Для прочного соединения волоконных матов между плоскими трубками успешно используется стандартный производственный процесс (пайка). Таким образом, достигается низкое сопротивление теплопередаче между адсорбентом и жидким теплоносителем. Паровые каналы обеспечивают достаточный массоперенос в процессе адсорбции и десорбции, см. рисунок 2. Большая площадь поверхности волокнистых структур и очень высокий коэффициент заполнения адсорбента: 333 кг адсорбента на м³ объема адсорбционного тепла.
обменник.
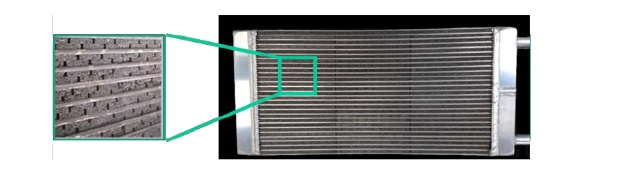
Рис.2 Волоконно-адсорбционный теплообменник.
Гибридный цеолит/графитовый адсорбер.
Ведущими принципами разработки инновационного гибридного цеолит/графитового адсорбера была возможность достижения высокой эффективности и высокой удельной мощности, обеспечивая в то же время гибкость и простоту реализации и сборки системы. Чтобы оценить жизнеспособность концепции, были проведены предварительные исследования на небольших выборках, как описано в [27]. Были изучены различные геометрии адсорбера, как показано на рисунке 3, а также механические и адсорбционные свойства гибрида после нанесения цеолитного покрытия.
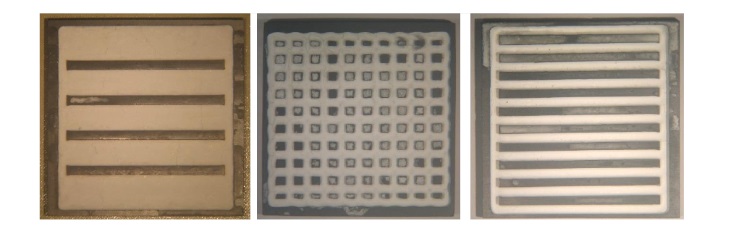
Рис.3. Три небольших образца гибридных цеолит/графитовых адсорберов: разная схема покрытия
По результатам этого анализа был спроектирован модульный теплообменник, показанный на рисунке 4. Он состоит из определенного количества собранных двусторонних графитовых пластин, двух компактных коллекторов, прокладок и винтовых зажимов. Каждая полупластинка состоит из технологической стороны (на которую осаждается цеолит) и стороны теплоносителя (HTF), по которой течет жидкая среда, обеспечивающая необходимую тепловую энергию для десорбции или для удаления тепла адсорбции. В конечном итоге две отдельные полупластинки соединяются вместе, образуя герметичный путь для жидкости, а компактные коллекторы позволяют распределять жидкую среду по каждой пластине. Одной из ключевых особенностей инновационного гибридного адсорбера является возможность изучить и спроектировать правильный путь HTF: высокая обрабатываемость графита позволяет простым и дешевым способом реализовать чрезвычайно сложный путь прохождения жидкости с конечной целью обеспечение равномерного распределения температуры на поверхности пластины. Действительно, равномерное распределение температуры в слое цеолита и уменьшенная разница температур между входом и выходом теплоносителя могут гарантировать оптимальные условия для явления адсорбции/десорбции.
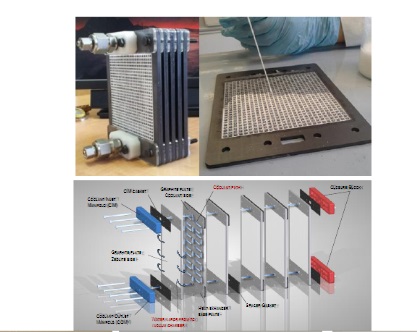
Рис. 4. Концепция графит/цеолитового адсорбера: собранный прототип (вверху слева); Покрытие адсорбентом (справа вверху), в разобранном виде (внизу).
Результатом анализа стал выбор двойного зеркального многозмеевидного поля потока в качестве распределителя теплоносителя. Количество параллельных змеевиков было спроектировано так, чтобы уменьшить падение давления жидкой среды. Проектирование было завершено тестированием различных возможностей склеивания и реализацией компонентов для соединения пластин [28]. Реализованный прототип показан на рисунке 4 вместе с процессом нанесения покрытия. В эталонном тесте в контролируемых рабочих условиях (90°C/35°C/15°C), проведенном в ITAE, зафиксирована плотность мощности 280–470 Вт/кг при времени цикла от 200 до 500 с.
Испаритель/конденсатор.
Разработка более эффективных адсорбционных тепловых насосов или чиллеров с термическим приводом также приводит к необходимости совершенствования концепции испарителя. Многие из имеющихся на рынке адсорбционных систем используют воду в качестве хладагента, для чего требуется – учитывая температурные условия от 3 до 20 °C – давление испарения от 0,76 до 2,34 кПа. Эти условия давления ниже атмосферного предполагают другие характеристики испарения по сравнению с обычными диапазонами давления и, следовательно, требуют соответствующей конструкции испарителя. Существующие испарители в имеющихся в продаже машинах часто используют концепции кипячения в бассейне или падающей пленки (например, Vaillant, Viessmann). Решения для кипячения в бассейне, например, с трубчатым змеевиком или трубчато-ребристым теплообменником, частично или полностью погруженным в бассейн с хладагентом, часто страдают от того, что эффективного режима пузырькового кипения трудно достичь при небольших перепадах температур, которые могут быть достигнуты. поставляется. Частично затопленные варианты весьма чувствительны к уровню заполнения, и только области трехфазной линии контакта теплообменника вносят значительный вклад в испарение. Концепции падающей пленки приводят к высокоэффективному тонкопленочному испарению благодаря очень небольшому термическому сопротивлению пленки хладагента, но для них требуется дополнительный циркуляционный насос. Поскольку важным преимуществом адсорбционной технологии является отсутствие каких-либо движущихся частей, следует избегать использования дополнительного насоса. Несколько недавних исследований в научно-исследовательских институтах и промышленности направлены на преодоление ограничений современных испарителей: В области пузырькового кипения исследуют характеристики образования пузырьков при испарении воды при давлениях ниже атмосферного, чтобы применить знания об основных механизмах кипения в усовершенствованной конструкции испарителя. Чтобы улучшить теплопередачу испарения в частично затопленных испарителях, иногда используют оребренные трубы или трубы с микроструктурированным/пористым поверхностным слоем. Таким образом, можно использовать капиллярный эффект для распределения хладагента в виде тонкой пленки, что приводит к значительному увеличению коэффициента теплопередачи. Еще одним новым подходом к разработке испарителя/конденсатора для адсорбционных модулей является периодическое использование только одного теплообменника в качестве конденсатора и испарителя. Пары хладагента конденсируются на теплообменнике на этапе десорбции и затем испаряются на этапе адсорбции с помощью того же теплообменника. Преимуществом этого подхода является уменьшение объема и сложности модуля, поскольку два теплообменника заменяются одним и можно избежать внутренних клапанов и т. д. С другой стороны, эта концепция включает в себя определенные проблемы, связанные с конструкцией теплообменника и подачей хладагента: поскольку теплообменник периодически колеблется между уровнями температуры испарителя и конденсатора, уменьшение термических масс (теплообменника и хладагента) до минимума необходимо для сохранения удовлетворительная мощность и эффективность модуля. Кроме того, особенно при работе с небольшими количествами хладагента, важно обеспечить хорошие условия контакта между хладагентом и испарителем. Накопление воды без контакта с теплообменником должно происходить, поскольку она больше не будет доступна для испарения. Одним из способов решения этих проблем является работа испарителя/конденсатора в режиме динамического тонкопленочного испарения и обеспечение большой площади поверхности. Во время конденсации хладагент удерживается непосредственно на поверхности теплообменника за счет поверхностного натяжения, что обеспечивает благоприятные условия смачивания для фазы испарения. Используя пористые структуры, можно увеличить емкость хранения хладагента за счет капиллярного действия. Тонкие пленки хладагента обладают очень малым термическим сопротивлением, что потенциально влечет за собой высокий коэффициент теплопередачи и, следовательно, возможность спроектировать компактный и эффективный испаритель/конденсатор. Однако характеристики динамического испарения очень чувствительны к геометрии теплообменника, свойствам материала и поверхности, а также условиям эксплуатации, как показывают исследования продемонстрировано на теплообменниках с оребренными трубками. Поэтому сложная конструкция теплообменника имеет решающее значение. Первые прототипы испарителя/конденсатора на основе волоконных структур (идентично конструкции AdHEX, показанной на рисунке 2) были разработаны и испытаны компаниями SorTech AG, Fraunhofer IFAM и Fraunhofer ISE в рамках проекта ADOSO, что дало многообещающие результаты.
Интеграция теплообменников в модуль.
Функциональность теплового насоса или чиллера может быть достигнута только при сочетании обоих теплообменников: для адсорбции/десорбции и испарения/конденсации. Комбинация тогда называется «адсорбционным модулем». Существуют различные возможности их комбинации, см. рисунок 5. Первая возможность заключается в том, чтобы иметь разные корпуса для всех теплообменников (ад/десорбция, испаритель, конденсатор), см. рисунок 5. Соединение осуществляется с помощью клапанов (активных или пассивных), которые контролировать поток пара на различных этапах цикла адсорбции/десорбции. Второй вариант – интеграция обоих теплообменников в один корпус. В этой концепции один теплообменник служит испарителем и конденсатором в модуле. Эта компактная конструкция означает, что как тепловая масса адсорбции, так и теплообменника испарителя/конденсатора становятся важными для производительности системы, поскольку теперь последний также должен циклически переключаться между температурой испарения и конденсации. Работа машины может осуществляться либо с одним модулем, работающим попеременно в режиме адсорбции и десорбции, либо с двумя модулями, работающими параллельно. Поскольку работа с одним модулем обеспечивает непрерывное производство тепла, но не холода, эта концепция используется только для тепловых насосов. Это дает возможность использовать различную продолжительность процесса адсорбции и десорбции, что может быть полезно, поскольку скорость десорбции обычно выше, чем скорость адсорбции. Такая стратегия работы приводит к увеличению плотности мощности. Кроме того, рекуперация тепла может быть реализована намного проще в рамках концепции двух модулей.
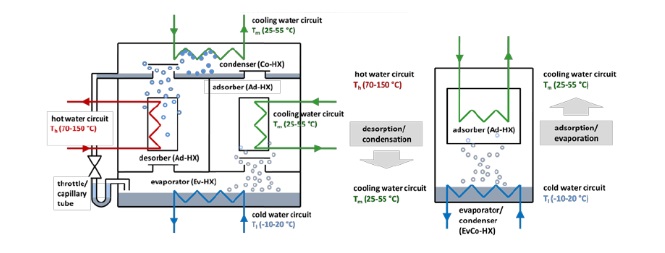
Рис. 5. Концепт адсорбционного модуля.
Из разработок теплообменников, описанных ранее, только концепция волоконного теплообменника в сочетании с прямым покрытием SAPO-34, разработанная в проекте ADOSO, до сих пор была реализована как законченный адсорбционный модуль. Два волоконных теплообменника одинаковой конструкции установлены в одном корпусе (как показано на рисунке 5 справа) с использованием запатентованной концепции SorTech AG, которая позволяет использовать очень тонкую толщину стенок, что приводит к снижению затрат и тепловой массы корпуса. Первые измерения прототипа одного модуля без рекуперации тепла были ранее. Установка двойного модуля со стандартным методом рекуперации тепла показала удвоенную плотность мощности по сравнению с продуктом eZea от SorTech AG без снижения COP, см. Таблицу 1. Два модуля (eZea и оптоволокно) показаны на рисунке 6.
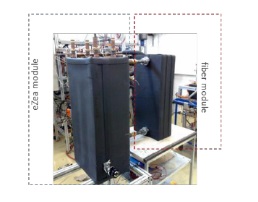
Рис. 6. Адсорбционные модули продукта «eZea» и прототип волоконного модуля.
Выводы
В конструкции адсорбционных тепловых насосов и чиллеров используются эффективные концепции теплообменников и адсорбционные материалы, которые обеспечивают высокое поглощение хладагента в диапазоне температур и давлений применения. Некоторые недавние разработки, посвященные концепциям теплообменников, показывают многообещающие результаты, которые теперь доступны для дальнейшего развития в адсорбционном модуле.
Сравнение концепций приведено в таблице 2. Волоконный адсорбер может достигать того же количества массы адсорбента на объем, что и пластинчато-ребристый адсорбер с самым толстым покрытием, тогда как концепция графитового адсорбера удерживает еще больше адсорбента. Соотношение масс между теплообменником и адсорбентом примерно одинаково для двух концепций со связующим покрытием, конструкция волокнистого адсорбера еще не оптимизирована с точки зрения массы металла. Прочно связанный тонкий слой адсорбента на волокнах обеспечивает компактную конструкцию с высокой объемной удельной мощностью. Вместе с новыми концепциями испарителей/конденсаторов, работающих в режиме динамического тонкопленочного испарения, и теплообменников с большой площадью поверхности, могут быть предусмотрены компактные адсорбционные модули для адсорбционных тепловых насосов и охладителей.
Таблица 2: Сравнение представленных адсорбционных теплообменников
Тип теплообменника Пластинчато-ребристый теплообменник с покрытием на основе связующего вещества Волоконный адсорбер с прямым покрытием Гибридный цеолит/графитовый адсорбер
Масса теплообменника [кг] 0,465 8,5 0,478
Масса адсорбента, сухая (кг) 0,062 – 0,543 3,3 0,5
Материал теплообменника алюминий алюминий графит
Адсорбент ТиАПСО SAPO-34 SAPO-34
Общий объем [дм3] 1,4 9,9 1,2
Общая масса на объем (кг/дм³) 0,38 – 0,72 1,19 0,81
Массовое соотношение (кгад/кгHX) 0,01 – 1,17 0,39 0,96
Коэффициент заполнения адсорбента (кгад/м³) 44 – 388 333 416